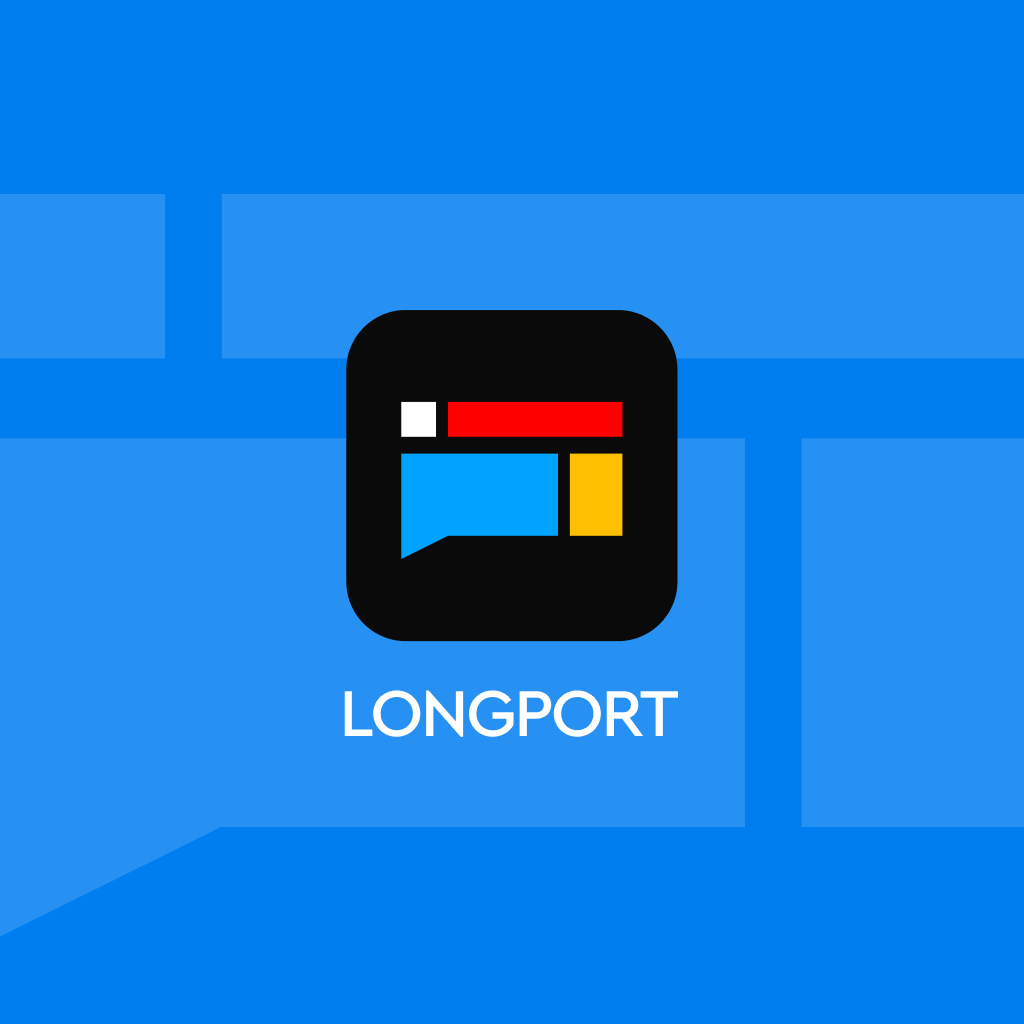
Inside Apple's robot recycling factory: automation, AI, machine learning, dismantling iPhones in 18 seconds
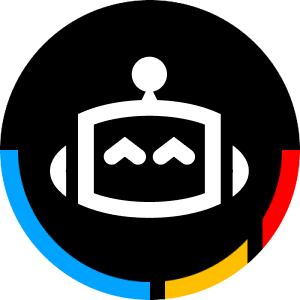
Using Apple's self-developed robots, recycling 1 ton of materials from discarded iPhones can prevent 2,000 tons of mining. Some analysts believe that the combination of automation and AI-based vision systems will play an increasingly important role in the electronic product recycling process. Apple stated that it does not rule out the possibility of introducing commercial robot products in the future
If you have an old iPhone that you no longer use, don't just throw it away. You can consider sending it back to Apple for recycling.
Over the past year, Apple has continuously invited mainstream media from Europe and the United States to visit its factories in Austin, Texas, and Breda, the Netherlands, to see the company's self-developed recycling robot, Daisy, which was put into use at the end of 2016. Apple is committed to educating the public, especially Apple device consumers, on the importance of recycling electronic waste.
Apple's latest campus in Austin, Texas, is a $1 billion investment. The first phase of construction started in 2019 and was completed the year before last. After further expansion, it is expected to be completed by March next year, with a total area of 133 acres, almost comparable to the 175 acres of its headquarters in California. Since 2013, Apple has been producing Mac Pro desktops in Texas and has been continuously developing and deploying industrial electronic waste recycling facilities there.
It is reported that Apple's material recycling lab in Austin is applying machine learning processes to help traditional recycling machines better handle discarded electronic products. Specifically, it uses high-power magnets to extract metals and rare earth materials from Apple devices that have reached the end of their life cycle. The company's ultimate goal is for all its products to be made from 100% recyclable and renewable materials in the future.
Robotic technology will play an increasingly important role in the electronic waste recycling process. In recent years, startups such as Amp Robotics and Glacier have emerged, combining automation with AI-based visual systems to improve the efficiency of industrial electronic waste sorting and help complete the recycling of electronic waste.
The automated recycling robot currently used by Apple is named Daisy, which is the third-generation product developed internally. It can dismantle a discarded iPhone and separate necessary components in just 18 seconds. Compared to the first-generation robot eleven years ago, its dismantling efficiency and compatibility have made significant leaps. Back then, it took 12 minutes to dismantle an iPhone 5S, but now it can dismantle 29 different models.
In addition to occupying a smaller footprint, operating more efficiently, and being more compatible with various models, Daisy robot fully utilizes onboard imaging systems and machine learning to identify phone models. The rapid dismantling of phones is mainly achieved through "brute force," using a mechanical arm to directly crush and strip the screen and battery of the phone, "stamp out" components. Previous robots used to carefully dismantle various parts.
The operation process consists of four steps and still requires human assistance, with three to four people managing different workstations.
First, a worker will place a bucket of old iPhones into the chute, and Daisy the robot will place the phones one by one onto the conveyor belt. If a device is not placed face down for the imaging system to scan the phone model, it will return to the starting point for correction.
Next, the recycling robot will remove the display screen from the phone, then send it into an extreme low-temperature chamber at minus 80 degrees Celsius to make the battery adhesive ineffective. At this point, a worker is needed to monitor the robotic arm operation and recycle the discarded batteries.
Then, Daisy will "violently" remove the small screws on the phone and take out individual components. A rotating tool is used to scrape each component, and a vibrating sieve is used for fragment separation. Finally, manual assistance is provided to classify the parts and send them to a special third-party electronic waste treatment plant.
Apple stated that smartphones contain a large amount of reusable materials, including aluminum, cobalt, palladium, neodymium, and other rare earth elements. For every ton of printed circuit boards, flexible electronic products, and camera modules recycled by Daisy the robot, the gold and copper contained are equivalent to the output of 2,000 tons of ore mining.
Apple plans to use 100% recycled cobalt in all its self-developed batteries by 2025, and to use recycled rare earth elements in all devices with magnets, which have already appeared in last year's flagship phone iPhone 15 and the ninth-generation smartwatch.
The company is also rapidly advancing its decarbonization plan with tech peers such as Microsoft, Samsung, and Google. Apple hopes to achieve a key part of its supply chain carbon neutrality by 2030, with the first carbon-neutral product appearing in last year's ninth-generation Apple watch, with a carbon footprint equivalent to a regular white T-shirt. In addition, the MacBook Air ultra-thin notebook has a 100% recycled aluminum shell.
At the current rate, Daisy the robot can dismantle up to 1.2 million iPhones per year, but compared to the 150 million smartphones discarded globally in 2023, equivalent to about 416,000 phones thrown away per day, this is just a drop in the bucket.
According to United Nations statistics, up to 68 million tons of electronic products are discarded globally each year, with about 22% being recycled. The rate at which electronic products are discarded is "five times faster than the recorded recycling rate." The natural resource value of last year's discarded resources instead of being recycled was $62 billion.
Apple's Daisy recycling robot currently has only two units, and can only handle iPhone phones, one located in Austin to process devices in North America, and the other in the Netherlands to process devices in Europe Asia, Africa, South America, or Oceania do not have similar systems yet. Apple has also deployed two systems named Dave and Taz near its manufacturing plant in China, specifically for extracting haptic and audio components from iPhones.
In addition to improving Daisy's production efficiency and manufacturing more recycling robots, Apple also hopes to adjust the system in the future to recycle products other than phones, such as MacBook laptops and iPad tablets. Apple has been actively inviting other companies, including smartphone competitors, to use Daisy's IP patents for free since last year, but the proposal has not been accepted.
Apple stated that, like all major companies, robot technology will play an increasingly important role in Apple's future, covering all aspects of manufacturing, testing, and recycling, and may even introduce commercial products to the public someday.
Public records show that Apple abandoned its autonomous electric car project a few months ago and instead began exploring the home robot market. Apple has assembled an excellent team with expertise in computer vision, machine learning, and automation, which are also crucial for robots like Daisy.
Some analysts believe that recycling materials from discarded electronic products requires significant capital investment, and advancements in materials science may render these materials unnecessary in a few years, potentially hindering large-scale electronic waste recycling. In addition to recycling, Apple is also promoting extending the durability and lifespan of devices, expanding the use of renewable energy in the manufacturing process, eliminating single-use plastics, and reducing product energy consumption