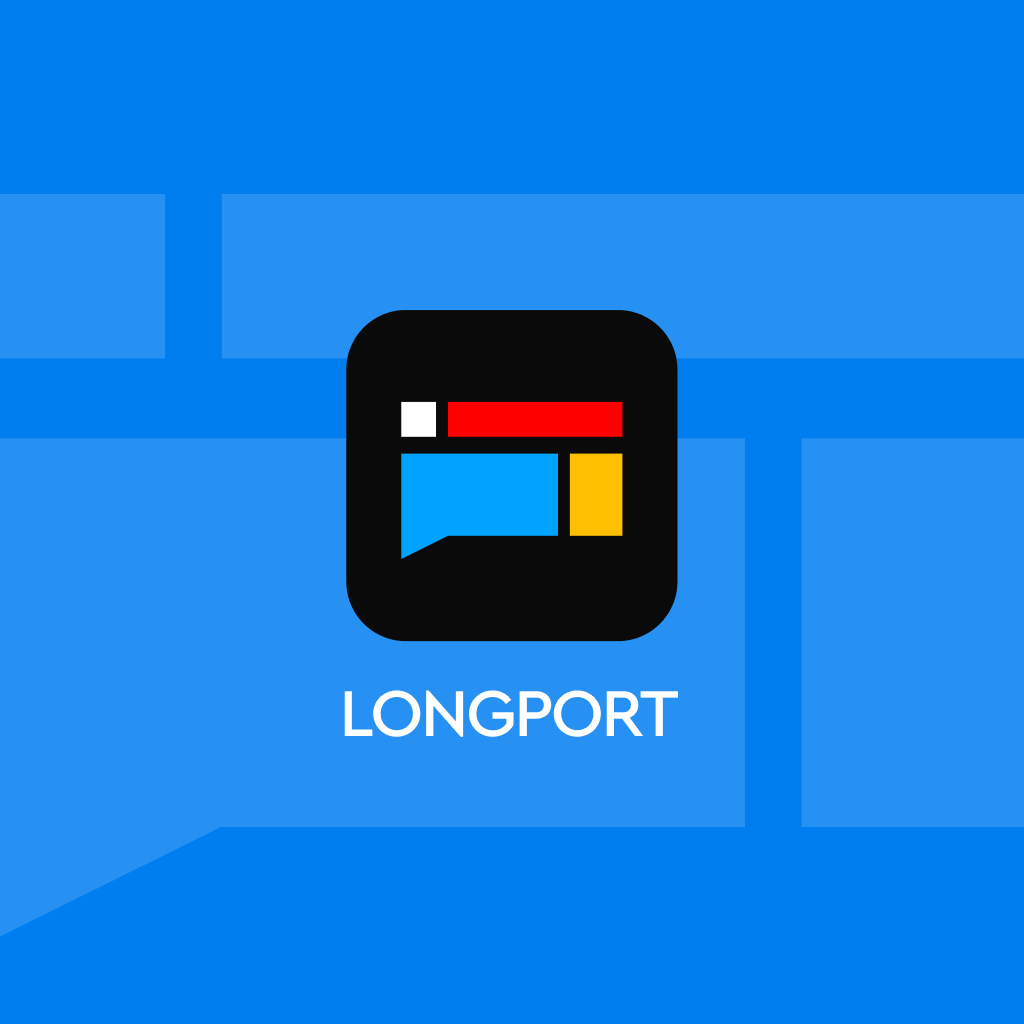
A $50 trillion target market! This blue ocean has caught the attention of Microsoft and NVIDIA
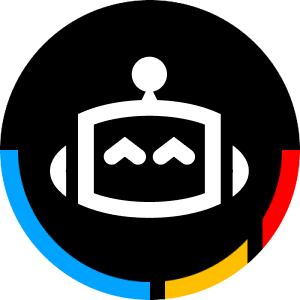
Engineers from NVIDIA have stated that the entire heavy industry is undergoing a large-scale transformation, which is happening through the construction of digital twin tools for physical spaces, with the help of AI to improve production efficiency and reduce costs. Before the factory is actually built, rapid iterations can be made in the virtual world, which is equivalent to "shining light from the virtual into reality", bringing about a significant change in the manufacturing production process
On Tuesday, May 21st, at Microsoft's annual Build developer conference, teams from Microsoft and NVIDIA demonstrated how their collaboration is leading the nearly $50 trillion global manufacturing industry into a new digital era.
Based on NVIDIA's Omniverse virtual reality and simulation platform and Microsoft's Azure cloud services, advanced digital twin tools can be developed to allow heavy industry engineers and developers to design, test, validate, optimize production lines, and automate various processes in a 3D virtual environment that accurately simulates the physical world before breaking ground on a factory.
It is reported that Microsoft and NVIDIA intend to digitize the $46 trillion global manufacturing process. The NVIDIA Omniverse Cloud API built on Microsoft Azure will bring data interoperability, collaboration, and important features such as physics-based visualization to software used for designing, building, and operating industrial digital twin tools.
For example, last year, Swedish company Hexagon AB connected its reality capture platform HxDR and manufacturing platform Nexus to NVIDIA's Omniverse platform, enabling enterprises to more easily develop and deploy digital twin applications, providing a full set of accelerated solutions for industrial digitalization.
To build an operational digital twin tool, designers will first use Hexagon's Nexus platform to design, build, and simulate products and industrial manufacturing processes. Factory designers will also use Hexagon's scanning technology to capture the real world and render it in a cloud studio.
Subsequently, engineers will use Rockwell Automation's Emulate3D digital twin software to simulate production systems before actual construction of the factory. Through NVIDIA's Omniverse cloud API, data from each application will seamlessly import into Microsoft's interactive data visualization software Power BI to generate a 3D environment in NVIDIA's Omniverse digital twin application.
Once the factory is built, its IoT data will be linked in real-time to NVIDIA's Omniverse digital twin tool in Microsoft Power BI. Combined with Microsoft's AI assistant Copilot, factory operators can gain a deep understanding of their production data using natural language.
In essence, the vision of Microsoft and NVIDIA is to jointly bring artificial intelligence and collaboration into the next industrial digital era Engineers from NVIDIA stated that the entire heavy industry is undergoing a large-scale transformation, which is happening through the construction of digital twin tools for physical spaces in the real world, aided by AI to improve production efficiency and reduce costs. Before the actual construction of a factory, rapid iterations can take place in the virtual world, which is equivalent to "shining light from the virtual into the real," bringing about a significant revolution in manufacturing production methods.
At a specific cooperation level, NVIDIA's RTX professional visual computing platform and accelerated computing technologies play a crucial role in building the aforementioned industrial digital twin applications, enabling large-scale simulations of the physical world to be presented in the digital world. Microsoft, on the other hand, helps manufacturing users extract data from edge industrial systems to the Azure cloud and utilizes AI for analysis to uncover value.
NVIDIA stated that Omniverse is a platform that connects and builds the industrial metaverse 3D virtual world based on the industry standard "Universal Scene Description OpenUSD." The universal scene description actually comes from the film industry, and unlike constructing a virtual scene referencing the real world in the film industry, its use cases in the industrial sector are basically "reversed," completing the construction and optimization of factories in a non-real world first, and then bringing them into the real world. This "non-traditional" approach actually deepens the utilization of data.
NVIDIA's team also mentioned that this transformation of manufacturing industry "shining light from the virtual into the real" will greatly transform remote monitoring and remote operation processes. For example, a multinational industrial enterprise can remotely view the operations of factories worldwide from its headquarters, or even remotely solve production-related issues in the real world, without the need to frequently send engineers on international business trips